Plant Maintenance
We support the stable operations of our clients’ plants with our technology and mobility.
Our plant maintenance division has been handling everyday
maintenance with the mission to support the stable operation of
clients’ plants all over Japan, including Mitsubishi Materials
Group.
Most of our offices are located next to Mitsubishi Materials Group
plants. We have established trusting relationships with the company
over decades of support and accumulated maintenance techniques. We
have been accumulating achievements while realizing the stable
operation of clients’ plants by correctly understanding what each
customer demands, thinking about how to solve problems with our
technologies, and gaining experience every day.
We fulfill our
missions with technology and mobility suitable for each customer and
their generation needs. Examples includes the improvement of safety
and quality of plant equipment, the evolution of safety
technologies, and care for the environment in order to create
sustainable societies. We contribute to both domestic and
international production.
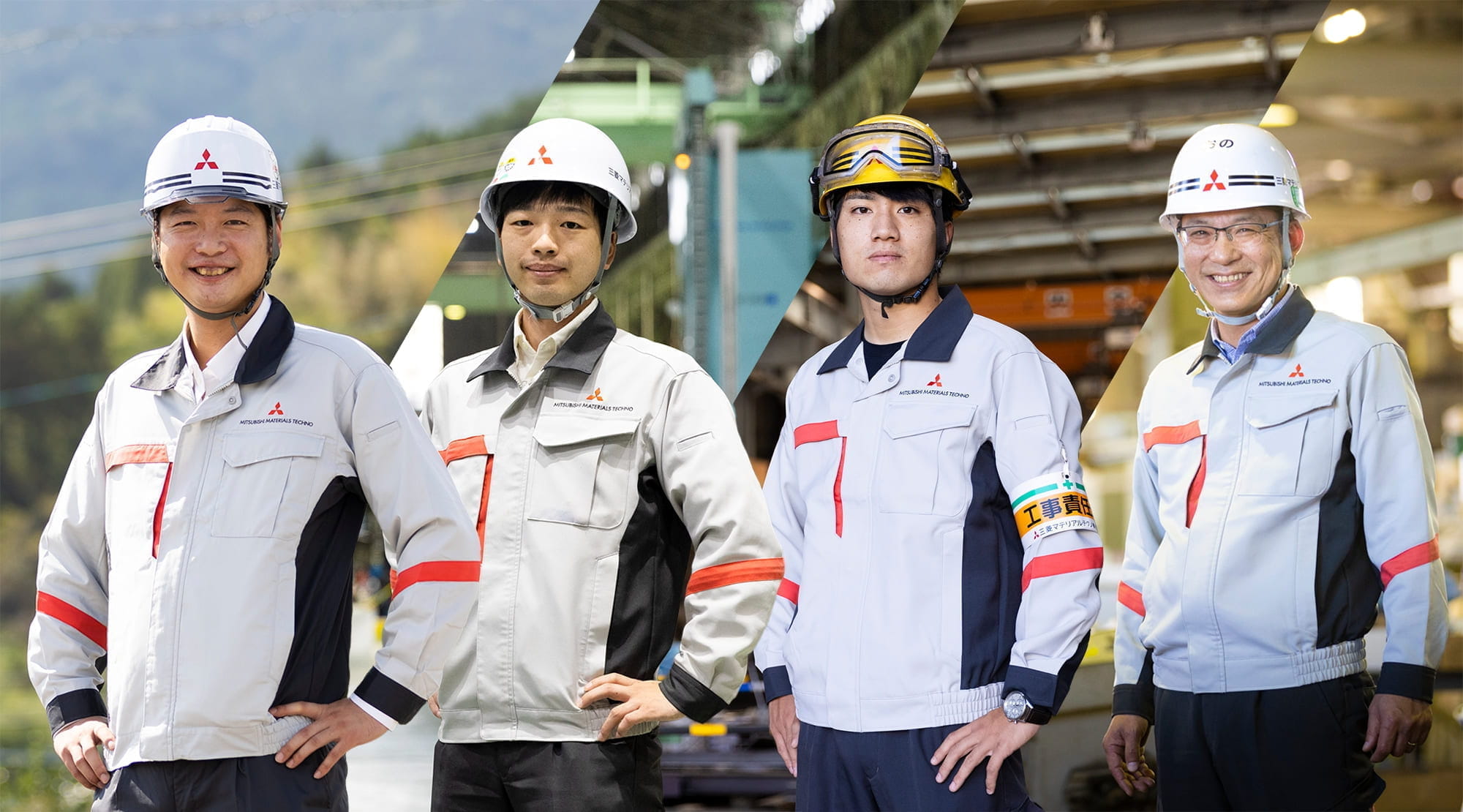
We accomplish the optimization of production equipment with great maintenance systems through our unique equipment improvement cycle.
Starting with the construction of new plants, our one-stop service handles post-operation repairs, planning for upgrades, construction work, and expansion and enhancement of equipment.
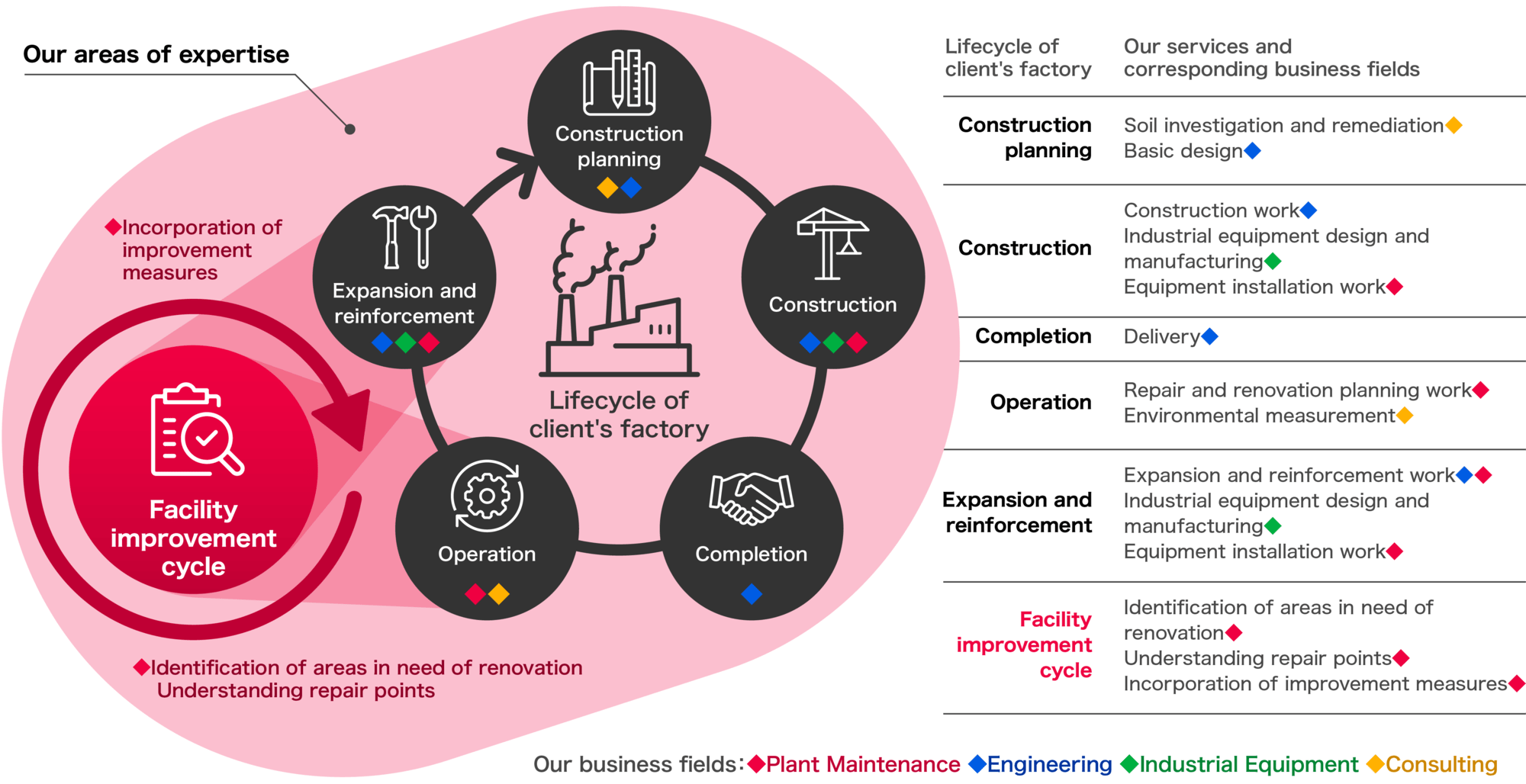
We continue to support clients’ plants collectively efforts as our engineering division handles new plant construction, and our plant maintenance division takes over for the project task. Through regular technical communication between our divisions, we identify areas to repair, including ease of operation and equipment parts to improve the plant's maintenance system in the long term. During the expansion and enhancement of construction, we suggest things to improve based on each client’s situation and keep the technology improvement cycle working to support the realization of a long-living plant with stable operations. We offer services to help negotiate with the government regarding environmental issues and legal compliances. We offer various consulting services, as well.
We provide maintenance services that meet each client’s needs.
Client needs in plant operations are extremely diverse. We provide repair and inspection services as needed to optimize the equipment maintenance.
Client needs
Our response
Our equipment suddenly stopped working. This will impact our business, so we would like to restart its operation as soon as possible!
We will perform quick repairs as an urgent treatment so that the operation can be restarted.
We want to pause operations for three days and have our equipment repaired so that it will have no issue with performance or function.
As a long-lasting measure, we will replace or repair parts of the equipment to bring back the original quality.
We will pause the operation of our equipment for a short period, during which we want to improve its production capacity and energy-saving system.
We will perform construction to improve the equipment’s safety, productivity, and convenience depending on each client’s needs.
Our facility cannot be shut down because it is a continuous operation. To prevent the any issues, we want to pause for repairs for a certain period once every year.
We will check for repairs with the client throughout the year and quickly perform equipment inspections and repairs in the plant during a certain period to prevent any issues.
We have a plan to improve our production capacity, but we do not know how to proceed.
With the support of our engineering division, we will work as one unit and provide a one-stop service for planning, design, construction, inspection, and trial operation.
We prioritize safety and health.
Our priority is the safety and health of everyone involved in the
project. At Mitsubishi Materials Group, we have a company code of
conduct stating “We prioritize safety and health over anything
else.” This is based on our philosophy that without an emphasis on
worker safety and health, workers and their families cannot enjoy a
stable and happy life. Without this, successful operation cannot be
expected and development of the company would not be possible.
“Safety and health is a top priority” is also stated in SCQDE*¹, the
decision-making guidelines established at Mitsubishi Materials Group
in 2018.
We are working on the establishment of both safety promotions and
organizational safety systems at each engineering office with the
goal to eliminate significant accidents and misconduct and improve
our technologies for maintenance work. We continue our efforts to
achieve zero accidents.
*1. SCQDE describes the order of priority for decision-making in the performance of duties, which are listed in the order of 1. Safety&Health (Safety and Health as a Top Priority), 2. Compliance&Environment (Legal Compliances, Fair Activities, Environmental Protection), 3. Quality (Quality of Our Products and Services to Offer Clients), 4. Delivery (Strict Adherence to Deadlines), 5. Earnings (Appropriate Profit).
Organizational Structure
We have instituted a safety department. Our plant maintenance division has placed about 20 safety staff members in each district. They communicate with the safety instructor at each branch to promote safety at the workplace.
Our Activities
- 1. Safety comes first
- Continuing education of general managers and education to workers given by the general managers to create environments built to prevent disasters.
- Promotion of safety activities for themes uniquely set by our safety instructors and workers. (PDCA)
- 2. Mutual Safety Patrol
- Appointment of patrols who are not on duty during regular hours to discover potential hazardous risks and improve the environment.
- Our safety mindset is to always think about better safety measures.
- 3. Reconfirmation of Safety Rules and Thorough Instructions for Adherence
- Unification of safety standards and rules and repeated education on common contents.
- Information gathering on revisions and additions to laws and regulations, internal notifications, and creation of countermeasure plans.
- 4. Improvement of Safety Skills
- Promotion of education and certification in safety knowledge.
- Safety workers must obtain certification as educational instructors to give special seminars to our and our partner company’s workers.
- 5. Ensure Hard-Copy Safety Policies
- When visiting an engineering office, we always check the safety policies and provide instructions and education to our and partner companies' workers as needed.